3D printing is changing the manufacturing. We provide innovative material solutions for a broad variety of 3D printing technologies. BASF products are the first choice for high-performance radiation-curable resins.
3D printing, also known as additive manufacturing, is a process of creating three-dimensional objects by layering material on top of each other. This technology has revolutionized manufacturing by allowing companies to quickly and cost-effectively produce complex parts and prototypes.
One of the biggest benefits of 3D printing is its versatility. It can be used to create everything from prosthetics to airplane parts, and it allows for customization and personalization that would be difficult or impossible with traditional manufacturing methods. Another benefit of 3D printing is its efficiency. Traditional manufacturing methods often involve wasteful processes, such as cutting and shaping materials, which can result in significant amounts of scrap. 3D printing, on the other hand, only uses the amount of material necessary to create the object, reducing waste and saving time and money.
3D printing is changing manufacturing by making it faster, more efficient, and more adaptable to specific needs. As the technology continues to advance, it is likely to become even more widely used and impactful across various industries.
At Forward AM, BASF lives the ambition to drive the industrialization of additive manufacturing. They offer end-to-end solutions that combine materials with engineering services along the complete value chain. They have developed a full range of services to support our customers, from design for AM and simulation of part behavior to post-processing the final part. They tailor solutions to meet specific needs across all AM technologies. Benefit from our years of experience to boost your competitiveness.
The Technology: Stereolithography / Direct Light Processing / Liquid Crystal Display
When talking about the different 3 D printing techniques, our Larolux products are dedicated for SLA, DLP and LCD printing. These techniques have in common that the object is printed out of a liquid bath of photosensitive polymers. By applying UV lights, the printed object is created layer by layer, from top to bottom – similar to the image we are using.
The Larolux products are not ready to use materials. However, they are the main ingredients when it comes to formulate the finished photo polymer solutions. Together with other raw materials, such as VMOX (reactive diluent) as well as photo initiators, a suitable photo polymer solution can be designed. BASF offers a wide range of more than 10 different resins – allowing to design the right properties. The end products can thus vary from hard/brittle to flexible, opening a huge variety of end products to be printed.
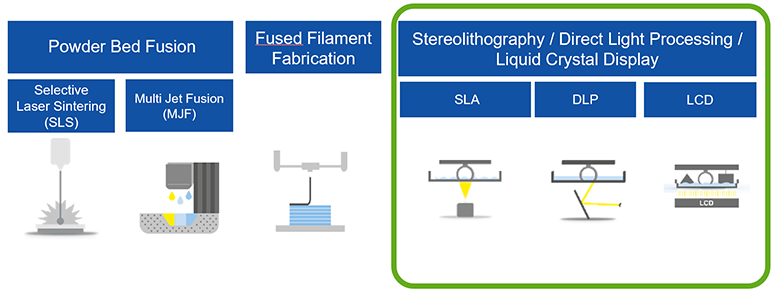
The newly created Larolux® range has been set up enabling you creating photopolymer formulations for UV curable additive manufacturing tailored to your needs. The Larolux® rage covers oligomers and monomers.
The new VMOX vinyl monomer from BASF combines technical advantages with an outstanding toxicological profile. Its excellent adhesion properties enable brilliant colours in printing inks and coatings.
VMOX is especially well suited for manufacturing UV-curing inks and coatings. For instance, it is used in digital UV inkjet printing as a reactive diluent. In such applications especially, the new vinyl monomer enables innovative coating formulations with a favourable toxicological profile. Alongside inks and coatings, VMOX can also be used in adhesives and 3D printing.
UV coating of printed material: one monomer, many technical benefits
- Low viscosity of around 4 mPas
- Virtually odourless formulations possible
- High reactivity with acrylates
- Good adhesion on all common substrates – even at low dosages
- High colour brilliance
Advantageous toxicological profile
According to the classification of the European Chemicals Agency (ECHA), VMOX neither constitutes a “serious health hazard” nor possesses “acute toxicity”. This labelling sets the new vinyl monomer apart from conventional products. Furthermore, VMOX is REACH-registered. “With VMOX, BTC offers an innovative vinyl monomer whose benefits are impressive on every level,” comments Juan Tortosa, Distribution Manager Business Iberia & Chemicals Europe, summing up the properties of the new product.
4-Hydroxybutyl Acrylate (4-HBA) forms homopolymers and copolymers. Copolymers of 4-Hydroxybutyl Acrylate (4-HBA) can be prepared with acrylic acid and its salts, amides and esters, and with methacrylates, acrylonitrile, maleic acid esters, vinyl acetate, vinyl chloride, vinylidene chloride, styrene, butadiene, unsaturated polyesters and drying oils, etc. 4-Hydroxybutyl Acrylate (4-HBA) is also a very useful feedstock for chemical syntheses, because it readily undergoes addition reactions with a wide variety of organic and inorganic compounds.